博客文章:您可以回收利用多少金属增材制造粉末?
Lucy Grainger
产品市场工程师 — 增材制造(金属3D打印)发布时间:2016年12月29日
为什么要回收利用?
对于任何生产过程而言,成品的质量都与所使用的原料的质量挂钩。对于使用金属激光熔融原理的增材制造 (AM) 技术,金属粉末的成分与用于处理粉末的机器参数密切相关。因此,粉末的化学与物理性质非常重要。制造商自然会对他们所处理的粉末状况是否可预测且稳定可靠非常关心。
这一问题也涉及到经济性。由于激光熔融所使用的精细金属粉末非常昂贵,因此应避免浪费。在大多数情况下,成型过程中使用的金属粉末实际上只有一小部分熔接到零件上,而大部分金属粉末并未熔融,因此还可以循环使用。
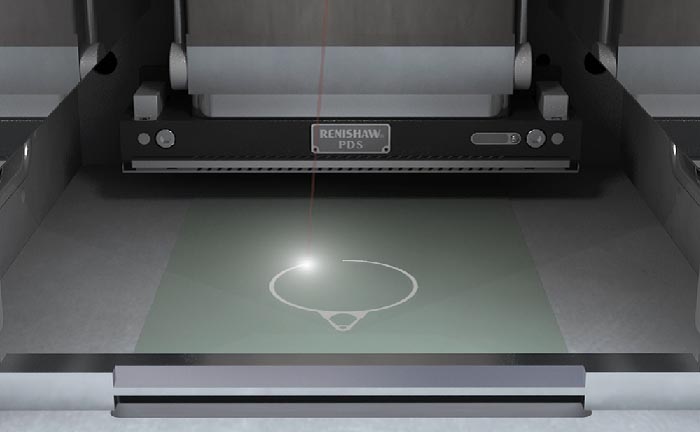
上图:每一成型层上通常只有一小部分粉末熔融,剩下的大部分粉末可回收利用。
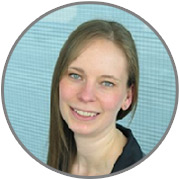
作者简介
Marc Saunders,增材制造应用总监
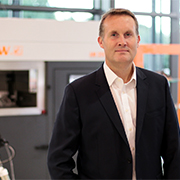
Marc Saunders先生在高科技制造领域有超过25年的丰富经验。Saunders先生在雷尼绍先后担任了多个职位,在开发公司屡获殊荣的RAMTIC自动化加工平台中做出了关键贡献,还成功为航空航天领域客户提供交钥匙测量解决方案。
Marc现在是雷尼绍全球增材制造解决方案中心网络的负责人,致力于帮助考虑将增材制造工艺纳入生产流程中的客户在采购新设备之前获得实际操作体验。
文档
-
White paper: Investigating the effects of multiple powder re-use in AM [en]
A single batch of titanium alloy powder was used over 38 builds using an AM250 additive manufacturing system. The powder and test parts was analysed for any changes in the chemistry and physical characteristics.
[4.3MB]
近净成型制造的优势恰恰取决于此类回收利用。如果我们非要认为未熔融的粉末已被污染而不适合回收利用,那么增材制造零件的成本可能会高得令人望而生畏。
激光熔融过程是否会降低粉末质量?
我们首先要考虑的是粉末的化学特性。我们正试图生产成分为高纯度合金的实体结构。增材制造设备供应商在竭尽全力创造一种惰性环境,以便能够在这种环境下存储活性粉末并进行激光熔融,这样金属合金在加热时不会形成氧化物或氮化物。
第二个需要考虑的问题是粉末的机械特性:我们需要可稳定流动的粉末,以便均匀分布在粉末床上。该“流动性”特征一般可利用霍尔流动性测试进行测量,并受粉末晶粒形态、粉末大小分布和存储密度等因素影响:
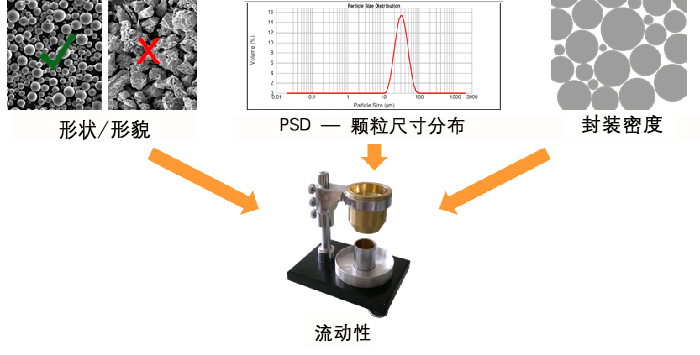
因此,我们需要考虑在进行激光熔融时,粉末的多次循环利用过程以及后续的粉末处理方式将使未熔融的粉末产生哪些化学和物理变化。
激光熔融期间,熔池受热速度极快,一些粉末将转化为合金的气态聚合物 — 一种由纳米大小的颗粒形成的薄雾。增材制造设备可利用气流吹走这些粉末床上的副产品,防止它们在粉末中聚积。
快速加热还可能导致较大的金属液滴从熔池中喷出,而粉末颗粒中残留的气体也可能会产生“飞溅物”。熔池边缘附近的粉末颗粒可能会熔融在一起,但并未附着到零件上,从而形成可能会影响粉末性质的不规则块状物以及“附属物”。
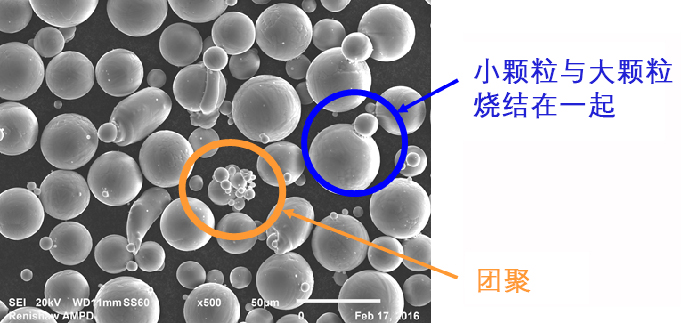
仔细选择加工参数,可限制“飞溅物”的影响,同时气流也将帮助清除加工区多余的副产品。为维持稳定的颗粒尺寸分布,粉末中未熔融的较大颗粒将被筛去。
评估粉末回收利用的影响
鉴于增材制造过程中粉末组分可能会发生的潜在变化,我们还有足够的信心来回收粉末吗?增材制造设备供应商采取的措施是否能够有效确保未熔融粉末的性质不受成型过程的影响?只有一种方法可以找到答案,那就是进行测试。
在增材制造常用的金属粉末中,钛合金最容易受大气中杂质的影响,而且是最昂贵的材料之一。这就使得钛合金 — 特别是常用的Ti6Al4V合金 — 成为研究粉末回收利用的理想选择。
回收利用测试程序
这项研究包括以下步骤:利用单个批次的粉末重复进行零件加工成型过程、清理每次成型后未熔融的粉末、筛分粉末,最后将粉末重新放回机器顶部的蓄粉仓。完成最初的几次成型后,将剩余的原始粉末处理好并放回蓄粉仓,因此,在研究结束时,最终成型件中的所有材料均已完成多个成型和筛粉周期。
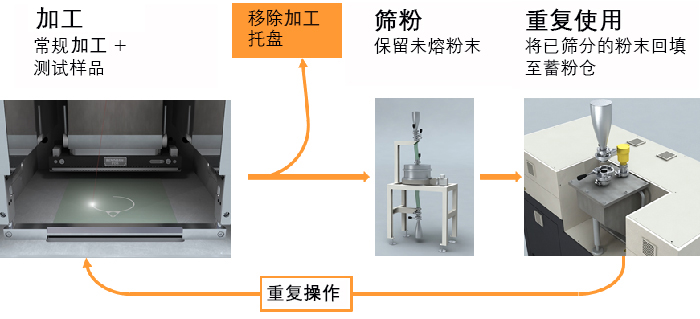
所有成型件均在一台增材制造机器上完成,包含各种几何形状的测试成型件和打样加工件。由于没有添加新的粉末,我们逐渐消耗完所有材料,在完成第38次成型加工后,剩下的粉末不足以再加工出合理尺寸的成型件。
从很多方面来说,这是一种极端的测试 — 在批量生产中,您通常不会连续回收同一批粉末,并一直消耗到粉末量非常少后,才添加新的粉末。因此,在更为正常的情况下,也就是在定期使用新粉末填满蓄粉仓的情况下,我们认为测试数据中的趋势将被减弱。
测试设备
测试在200 W激光功率的雷尼绍AM250系统上进行。AM250的一个重要特征是成型舱的良好密封性,它能够在成型过程开始时将成型舱中的气压降至0.05 bar,以除去水分、氧气和氮气:
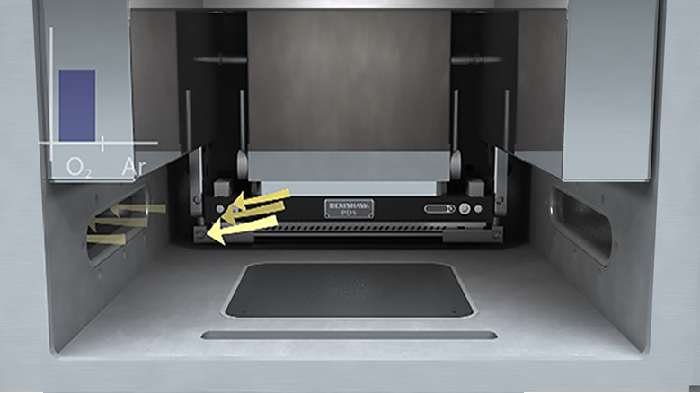
随后向成型舱回填氩气,快速创建一个适合加工活性粉末的惰性气体环境:
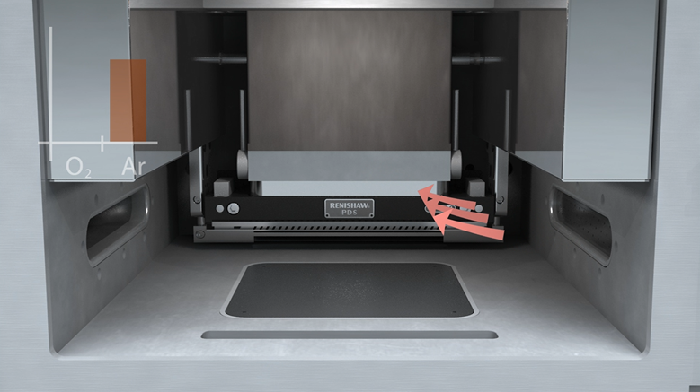
密封舱体同时意味着在成型过程中,AM250系统只消耗非常少的氩气 — 每小时仅为10升。粉末的筛分在一个外部装置上完成,也处于氩气环境下。
我们的测试方法是直接检测粉末的化学和物理性质,同时通过测试一系列成型件样品,评估使用回收粉末制成的零件的质量。我们在每次成型过程中包含了一系列测试样品:
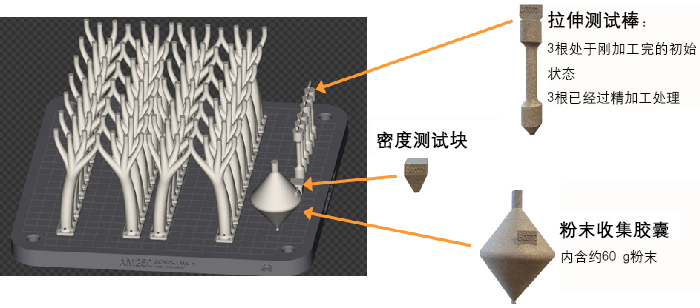
结果 — 化学方面
钛合金被划分为几个等级,每个等级根据间隙元素和合金元素的最大允许密度进行划分。其中,间隙元素 — 氧和氮 — 是最关键的因素。从密封容器中取出原始粉末样品,测量氧气和氮气浓度水平来跟踪这些杂质的积聚情况。
含氧量测量结果的趋势图(下图)呈稳定增长趋势,但是在第16次粉末回收之前,浓度值持续低于严格的超低间隙 (ELI) 指标(0.13%或1,300 ppm),并且始终不超过2,000 ppm的5级限制。
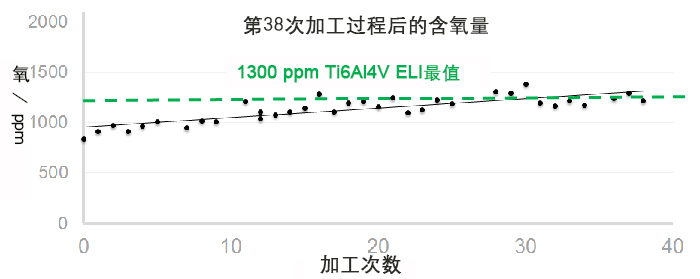
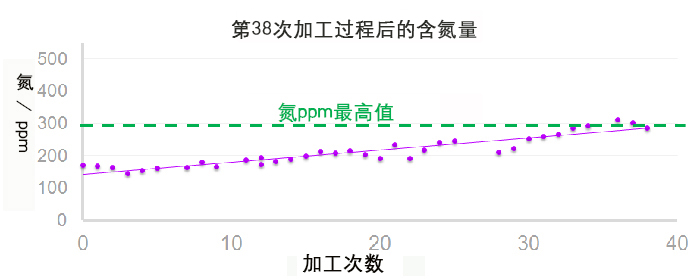
因此,假若严格控制空气环境,氧氮积聚水平也将降低。请注意,在多数“实际”情况下,可通过使用新的原始粉末定期填满蓄粉仓来减少这些影响。
结果 — 物理方面
扫描电子显微镜 (SEM) 分析了每次成型后从密封容器中提取的粉末,直观显示出晶粒形态和颗粒尺寸分布的所有变化。我们分析发现在整个回收利用期间,较小的粉末颗粒普遍减少。
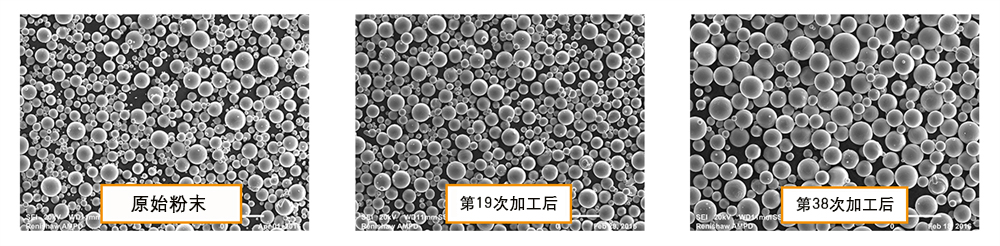
尽管可观测到精细颗粒的数量发生减少现象,但我们看到粉末形态只有非常微小的变化。较小的颗粒去哪了?它们很有可能烧结成了较大的颗粒,随后它们可能因变得过大而在筛粉期间被清除。
当我们转而分析颗粒尺寸分布时,可以看到图片显示的结果非常稳定,只有中等颗粒尺寸有稍微增加的趋势:
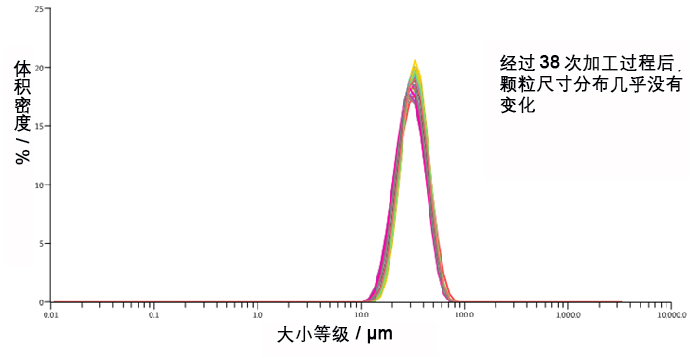
根据分布图所示,吹气和筛粉操作相结合,应该能够清除大部分尺寸过小或过大的颗粒(这恰是其设计目的)。
其中一个有趣的结果是颗粒尺寸分布与气流之间的关联性。下图显示了在霍尔流动性测试下中值颗粒尺寸 (D50) 和流速是如何相互对应的。中值颗粒尺寸随着流速的缓慢增加而缓慢增长。在霍尔流动性测试中,所有粉末均可十分容易地流动,除了原始粉末由于其过于精细,需要轻轻敲打一下以使其流动。
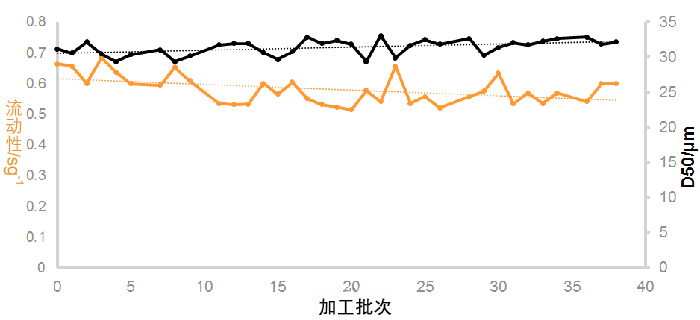
结果 — 物理性质
对所选样品进行抗拉测试,包括刚加工完初始状态的测试棒和经过精加工处理的测试棒。按照适用于雷尼绍医疗植入体的热处理条件,将样品放到真空炉中进行热处理。
正如预期那样,经过精加工处理的拉伸测试棒比刚完成增材加工的样品的抗拉强度稍高。鉴于在试验过程中间隙氧元素和氮元素的浓度逐渐增加,可以预料极限抗拉强度 (UTS) 会随着成型次数增加而增大。
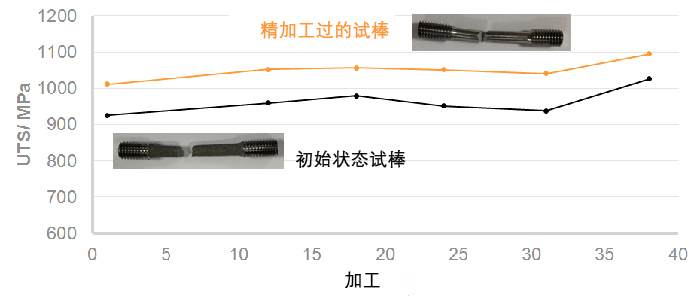
这些结果是否也适用于其他机器和材料?
保险起见的回答是“不一定”。
每种增材制造系统建立惰性环境和处理粉末的方式稍有区别,这可能对回收利用过程中的粉末变化产生一定影响。
根据其化学吸收性质,钛提供了吸收大气中的杂质(如氧气和氮气等)的最差情况。然而,多次回收利用可能会影响钛合金以外其他材料如铝、不锈钢和钴铬合金等的形态。
简而言之,若想完全鉴别这些影响,则需要对一系列材料和增材制造平台进行更多的研究。
摘要
令人欣慰的是,粉末的重复回收利用似乎不会对钛粉状况造成不利影响,至少在雷尼绍AM250系统上可以做到这一点。
我们发现,粉末的化学性质和物理性质一般会有变化,但并不明显。在这些惰性条件下,化学性质的下降程度较低,而“流动性”实际上会随着回收利用而有所提高。气流和粉末管理系统可以有效地将成型过程中产生的任何过小或过大尺寸的颗粒从原料中清除。
这是对粉末在增材制造过程中如何受回收利用影响的一种极端研究:定期用新的原始粉末填满蓄粉仓很有可能会减缓粉末的化学和物理性质下降的程度。
对于大多数应用,似乎没有必要废弃未熔融的粉末。