成功加工纯机械切削零件需要具备哪些条件?
除设备加工能力之外,操作人员的经验以及对整个工艺制程的设计也是影响生产效率的重要因素。
本文改编自《Modern Machine Shop》杂志,已获原刊编者正式授权
© 版权所有 Gardner Business Media, Inc.
如果采用铸造方法加工零件,一般可以保证如期交付,但确实存在极少数延期交付的情形。R&D Manco公司是位于美国亚利桑那州凤凰城的一家机械加工分包商,为航空航天工业的众多知名客户提供服务。它加工的零部件通过了相关标准的认证,包括飞机燃料和控制系统使用的高精密组件。零件从铸件毛坯开始加工,一般交货周期为32周。但是,如果R&D Manco能够从实心坯料块直接切削出零件的精确形状,从而完全绕开铸造工序,则通常可以将客户期望的整体交货时间缩短60%以上,并且零件加工成本一般也会降低20%。因此,R&D Manco制定了一项长期目标 — 并且十年如一日地不懈努力 — 将尽可能多的零件从铸造加工过渡到纯机械切削加工。
他们的努力也得到了客户的支持与鼓励。一家重要客户在他们的一些加工合同中经常会附加一项要求,表示如果工厂有能力做到的话,可以自行选择使用铸造方法还是纯机械切削方法生产零件。另一家同等规模的客户甚至还拥有一个切削制程团队,专门负责分析将铸造加工转换成纯切削加工的可行性。然而,并不是所有零件都适合通过切削方法制造,比如某个交货周期为一年的零件,由于其具有较深的凹陷形状,而工厂(目前尚)无法通过机械加工做出这种形状,因此可能无法转换成纯切削方式。但是随着时间的推移,R&D Manco已经能够将一半曾经需要铸造加工的常见零件改造成纯机械加工制造。
绕开铸造工序后,客户的供应链得以进一步整合,工厂也可以承接供应链上的更多业务。
然而,随着纯切削加工趋势日渐明显,这种加工方法也受到更多其他因素影响,这与工厂越来越重视相关加工作业有关。工厂在决定采用纯切削方法制造零件时不仅仅是增加铣削作业,绕开铸造工序后,客户的供应链得以进一步整合,工厂也可以承接供应链上的更多业务。工厂在决定最终成本和零件交货周期方面发挥着愈加重要的作用。它必须承受进一步缩减成本和缩短交货周期带来的全部压力。简而言之,采用纯切削加工方法的工厂注定需要付出更多努力。
因此,除了机床的加工能力之外,R&D Manco的生产方案中至少还有其他两个因素对于其在纯切削加工方面取得持续成功也很重要。一个是操作人员,另一个是工艺制程。针对纯切削加工,工厂致力于培养相应的企业文化和能力,以实现不断提高金属切削率的根本目标。
-
过去,这样的零件会从毛坯铸件开始加工。如果R&D Manco能够成功地将生产过程转换为从实心坯料块开始直接切削出零件,就一定可以为客户缩减成本并缩短交货周期。但是,要做到这一点,他们注定要承受更大压力,也必须付出更多努力。
-
纯机械切削加工对R&D Manco最基本的能力要求是五轴加工技术。R&D Manco拥有六台Haas Automation制造的五轴加工中心。
-
他们在纯机械切削加工方面取得成功的秘诀中有一条必不可少:鼓励经验丰富的机械工程师不断改进和优化工艺制程 — 这已成为一种企业文化。
-
纯机械切削加工会完全取代铸造加工吗?不会。有些零件仍然需要采用铸造加工方法。就拿这个零件来说,机械切削加工无法制作出这种内部形状。虽然R&D Manco可以将铸造加工转换成纯切削加工并使客户获益,但是,对于许多加工任务来说,铸造方法依然是最理想的选择。
竞争文化
R&D Manco拥有两家毗邻的工厂,总面积达3万平方英尺,员工人数超过70人。这个不同寻常的名称来自最初Manco和R&D Specialty两家工厂的合并。这两家工厂很早以前就已经合并了,但这个组合式的名称却保留至今,其中部分原因可能是仍有许多员工曾亲历了当时的过程。
“我们聘请了一些经验极其丰富的机械工程师,”Bloom先生说。经验对于工厂成功发挥五轴加工的优势非常重要。持续不断地从铸造加工转换到纯切削加工,这意味着工厂需要定期设定新的工艺制程,以突破原始设计,通过铣削制造出具有复杂、有机形状的零件。在开发此类加工工艺时,几乎总会出现理论设计与实践经验技能相交汇的一点。例如,在模拟加工中看似可行的五轴铣削循环在实际操作过程中可能会受到噪声或精度超差的困扰,这是因为工件位置设定不够精确,导致无法沿特定轮廓走行刀具等等。在这种情况下,听从经验丰富的加工团队成员的意见,通常可以找到最有效的方法来改进制程,从而以最好的方式解决问题。
公司管理层向生产人员明确指出,这种经验判断非常宝贵。事实上,不断进行此类性质的制程改进意义重大。毕竟,针对一个零件换用纯切削加工方式最重要的原因之一便是这种方式能够不断提高加工效率。为促进实际生产经验在不断改进工艺制程方面发挥更大的作用(即提高金属切削加工的速度和效率),工厂有意在员工当中培养一种竞争文化。实际上,这种文化发挥的作用最明显的表现领域可能不是五轴加工,而是工厂的50锥形主轴加工设备。在这一领域中,工厂投入使用了大型、重型的加工中心,目的是最大限度地提高铝材和钛材切削加工过程中的金属切削率。与其他领域一样,工厂鼓励该领域的机械工程师与编程人员一起合作探讨更多切削路径和切削刀具选项,以不断改进制程工艺。50锥形主轴设备加工的不同之处在于,机床的加工效率有时可能实现显著提升,特别是加工铝材时。比如一个被工程师昵称为“三球”(因其形状得名)的铝制零件,在采纳了员工在进给速度和切削深度方面提出的多项改进建议后,在第一个加工循环期间便可去除此工件几乎90%的初始原料,而所需时长也从八个多小时缩短至两小时四十三分钟。而促使这些改进发生的驱动力则是为了超越自己以往的成绩,甚至是(良性)超越他人。
当有人冲破束缚、成功创新时,我希望其他人也勇于效仿,敢于突破。
Bloom先生(R&D Manco公司)
当然,众多工厂都对经验丰富的机械工程师求贤若渴。但是,这些拥有宝贵经验的人才已经越来越稀缺了。R&D Manco也面临同样的挑战。为了充实人才储备,期待他们将来能够运用不断积累的丰富经验做出贡献,工厂根据美国模具与加工协会的培训课程制定了一项学徒计划,目前已有三名员工加入了该计划,将来会有更多的员工加入。该计划中有一个亮点,即员工接受培训的起步领域。在我们工厂,每位员工都是从工件检测领域入门,Bloom先生说。没错,我们的目标是要不断缩短加工循环时间和交货时间,为此我们还营造了竞争性的企业文化,目的就是鼓励员工努力实现这一目标。但是,要实现目标,首先要充分理解目标,这一点更为重要。也就是说,R&D Manco的每一名员工首先要了解合格零件的标准。
运用机床监控,把握制程能力
机床监控是R&D Manco公司取得成功的另一个重要因素。采集机床状态基本数据,分析数据以诊断并纠正切削中断的原因,这是工厂提高加工能力最重要的手段之一。工件切削与机床监控之间的关联可能并非一目了然,但事实上,它们之间确实存在着直接的联系。这种联系可以归结为一点:每当R&D Manco在某个零件的加工制程中绕开铸造工序时,就意味着突破了一个曾经阻碍零件制造效率的巨大瓶颈。然后工厂就可以将注意力转向纯切削加工过程中新出现的其他瓶颈。
实施机床监控的第一步是正视机床利用率 — 这一数字一度低得令人失望。
R&D Manco的许多机床都购自Okuma。公司指出,这些机床是实施机床监控的宝贵对象;利用制造商基于Windows的控制器,系统能够轻松地从机床收集实时状态信息。对于老式机床或制造商未提供此开放接口的机床,公司采用来自Shop Floor Automations公司的MTConnect适配器对机床控制器进行了改造,以便将这些机床也纳入整个工厂的机床监控系统之中。Predator公司的软件能够整合这些机床数据,将其整理后输出为图形和报表,供工厂随后进行分析。
实施机床监控的第一步是正视机床利用率 — 这一数字一度低得令人失望,公司管理者如是说。对于机床有效切削时长而言,几乎所有工厂都犯了同样的错误:他们主观认定的时间都要比机床实际切削时间更长。不过,了解实际的机床利用率会非常有帮助,即使这一数字可能令人失望,Beach先生说道。首先,这个指标可以让工厂了解自身实际加工能力。用于生产规划的企业资源规划 (Enterprise Resource Planning - ERP) 软件不一定了解这一点,这就是为什么即使已经在ERP中制定好生产计划,零件还是会延迟交货的原因。了解实际能力能够让工厂知道何时需要将业务外包出去,从而弥补工厂自身加工能力的不足。第二,了解实际利用率能够让工厂看清改进的潜力空间,继而着手努力挖掘这一潜力。
这项工作并不一定简单,但我们也不会特意将其复杂化。Beach先生说:“我们第一次开始实施机床监控时,各种各样的识别代码纷纷跳出来提示机床停机的原因。”电脑屏幕变成了一个五颜六色的调色板,显示着识别出的(或者软件认为识别出的)各种各样机床停止切削的原因。“原因多到令人眼花缭乱,却没有太大的价值,”他说。他得到的机床未切削的分析数据并不能很好地解释机床上实际发生的情况。相反,他意识到,实际上“未切削时间就是未切削时间,仅此而已”。在任何情况下,如果某种状况发生过于频繁,就应该找出原因并予以解决。如今,工厂的机床监控系统可以使用三种状态而不是两种状态(切削和非切削)对所有机床的所有活动进行描述。其中一个导致生产延迟的原因经证明其影响颇为显著,值得将其记录下来并加以监控。
这个原因就是首件检测。实践证明,首件检测的等待时间是导致工厂生产中断最重要的原因。这一发现可能是执行机床监控最早取得的主要成果之一。了解了问题所在之后,工厂采取了各种措施来解决问题。质检室增加了一台坐标测量机和一名技术人员,专门负责首件检测。此外,R&D Manco还在探索在工件无需离开机床的情况下执行首件检测的可能性。借助雷尼绍的“Productivity+”软件,机床自身便可通过测头对工件进行测量,并将测量值与原始CAD文件数据进行对比。部分工件种类已成功转为以这种方式完成首件检测,从而无须再将加工出的首个成品件送往质检部进行检测,因此完全避免了生产延迟。
机床监控实现的其他成果
Bloom先生和Beach先生指出了工厂通过机床监控获得的有关提高加工效率的其他各种发现,如果不是监控生成的数据令这些发现更为清晰明了,工厂管理层就不会这么快掌握它们。R&D Manco总结出的经验如下:
- 卧式加工不仅适合某些工件类型,也是一些加工种类的理想之选。工厂于2017年安装了一台配有六个交换工作台的卧式加工中心,但是最初的利用率并不十分理想。Bloom先生认为,问题在于工厂主要考虑的是这台机床的加工能力。工厂将加工作业分配给这台卧式加工中心,看重的是它可以很好地利用四轴完成加工。在当时,这种做法固然很好,但仅考虑加工能力就会忽视这样一个事实,即机床的生产效率实际上取决于操作人员当天可以设定的加工作业数量。对于卧式加工中心而言,最适合的加工作业就是那些因为加工的重复性特点而可以保留初始设定的工件。因此,一开始工厂在给机床分配工作时考虑的是加工能力,但现在会综合考虑加工能力、订单数量以及该作业是否是确保合同连贯执行所必需的关键部分等因素来合理安排机床的加工任务。
- 大型工件的搬运难题是制约生产效率提升的一大因素。例如在一个双机床加工单元中,如果被车削的工件太大而无法实现人工搬运,那么此时对加工性能进行数字化分析后,便会发现只需购买一套技术含量很低的硬件设备,便可大幅提升整体加工性能。当工厂发现将工件从该加工单元的一台机床搬运至另一台机床所需的时间甚至比预期还要长之后,他们为专门为这两台机床服务的起重机安装了一套龙门导轨,从而解决了这一效率问题。
- 关于七轴车削加工单元利用率的问题,有一种说法是正确的。为了执行最复杂的车削作业,工厂建立了一个由三台七轴车削中心组成的车削加工单元。鉴于这些机床的加工自动化程度如此之高,只需一次铣削循环即可完成整个工件的加工,所以大多数人认为一名操作人员便足以管理所有这些机床的生产作业。然而有些人并不同意这种看法;工厂管理层中持不同意见的人认为,实际上由两名操作人员负责该加工单元是较为合理的。这种争论可能会无限期地持续下去,直到机床监控数据最后给出了定论。在该岗位配置两名操作人员的做法是正确的。该加工单元的机床利用率是工厂所有设备中最低的(它们的利用率本来应该是最高的),而增加人手则大大提高了该单元的加工效率。
R&D Manco现有一名员工专门负责总结更多此类生产经验,其制造工程师Luis Hernandez被任命为公司持续改进团队的负责人。通过上述的调查与分析得出的结论显著提升了工厂设备的利用率,由此产生的潜在回报无疑证明组建这个团队是值得的。公司表示很需要像Luis Hernandez这样的角色,因为导致某一时刻发生生产中断的最根本原因并不总是那么显而易见,很可能是多个因素共同作用的结果。事实上,Hernandez先生并不是孤军奋战。他的一部分工作是听取他人的想法与意见,与团队成员深入探讨有关机床加工中断的问题,以便找出可能的原因和解决方案。他说:“我过去主要与工程技术部门沟通,现在我更多的是与车间领班们交流。下一步我将与机械工程师本人讨论数据,希望确定给他们的工作造成障碍的加工延迟原因。”
Bloom先生最后指出,这种分析数据和改进效率的做法同样适用于生产车间以外的场合。他说,这种做法也适用于办公室工作,例如向客户报备生产计划。甚至早在实施机床监控之前,公司就已经意识到,必须从“我们的事先报备情况对比我们的实际完成情况”的角度定期分析总结已完成的工作,他特别强调了它的重要性。他最近在这方面吸取的一个经验教训是:公司在钢件生产计划报备上过于冒进。事实上,钢件的实际加工速度无法满足工厂预先制定的生产进度。这方面的工艺流程可能还有待改进,不过目前由于在制定生产计划时将预期切削率调低,因此钢件生产报备的准确度提高了。
当客户询问一个未完成的生产订单的状态时,公司通常会发现当完整收集到回答该问题所需的所有信息时,答案可能已经过时了。
实际上,如果仅仅为了获取这些所需的信息,这一过程也将导致效率低下并浪费时间。他说,Bloom先生早在大约七年前就意识到了这一点。当客户询问一个未完成的生产订单的状态时,公司通常会发现当完整收集到回答该问题所需的所有信息时,答案可能已经过时了。信息太分散了,涉及的范围也过于广泛。
当时,他与一位软件开发人员合作开发了一款他称之为“Grand View”(大数据视图)的软件,这款软件可以快速提供足够的信息,用于回答客户的询问。该软件所需的某些数据可在工厂的ERP系统中找到,另一些则可在本地电子表格中找到。也就是说,这个自定义实用程序整合了多个不同系统的数据。他说,在使用了一段时间之后,他开始意识到这个统一的视图工具是多么有用,不仅可以用来回答客户的问题,还可以帮助自己更好地理解各种导致生产中断的原因,并且能够协助监控工厂日益复杂的工艺流程 — 尤其是在交货期要求越来越严格的情况下。
过去,以切削铸件为主的加工作业极少需要像现在这样多的流程控制工作。无论工厂的生产能力如何,等待铸件完成的时间都会导致冗长的成品交货期,工厂只有在收到铸件后才能开始加工。如今,情况不同了。现在,更多情况下,生产作业从开始到结束都由R&D Manco自主掌控,公司完全要对所承诺的更短工期和按时交货负责。责任增加意味着需要实施更全面的生产监控,因此,Bloom先生改进了他的Grand View实用程序,以满足这一需求。通过查询ERP系统的数据库来提取工件的加工循环时间,该自定义实用程序如今可自动计算并向管理层汇报最晚必须何时开始加工此工件,以确保满足承诺的交货时间。通过查询工厂的数字库存记录,该实用程序现在也可以显示库存是否充足或者是否需要补充库存。
这些都是很容易被忽视的重要信息。对于将客户供应链中的更多环节整合到自身业务范围内的工厂而言,对其提出的一个要求是,必须有一套日益成熟的系统,能够保持信息条理清晰、访问便捷,以便即使当工厂作业繁忙时,工作进展情况仍一目了然。
请访问www.renishaw.com.cn/machinetool,了解有关雷尼绍机床测头系统和软件的更多详情。
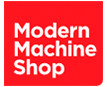