激光尺 — 一项能够精确加工40 m复合材料工件的功能性技术
Flow International Corporation(福禄国际股份有限公司)为其复合材料加工中心 (CMC) 选用了雷尼绍HS10和HS20激光尺。激光尺可为长度达40 m的复合材料面板持续一周的加工提供高达百万分之一的X轴移动精度。
Flow International Corporation的复合材料加工中心 (CMC) 对40 m长复合材料机翼蒙皮的单次安装加工一举获得成功,而在长达一周的加工周期中,保持长轴精度的关键因素之一就是雷尼绍HS10/HS20激光尺。激光尺及其组件RCU10实时补偿单元的测量距离的精度达到激光干涉仪的水平,在CMC的X轴上可实现百万分之一的定位精度。
CMC是Flow开发的一种新型机床,旨在满足航空航天工业生产尺寸偏差极小的大型工件的需求。“减少工件尺寸偏差是整个行业的目标,”Flow航空航天部门总监Mark Saberton解释道。“目的是减少装配时间、工作量以及机床加工。OEM希望消除装配过程中因为需要修配而增加产品负荷和延长加工时间的问题。他们希望送到装配车间的工件无需使用夹具和垫片就能够达到装配公差要求。重量也是一个问题。减少飞机工件的偏差可确保更好地控制飞机的最终重量。”
Flow生产的CMC机器是通过高压处理来加工复合材料工件的一站式加工中心。该类机床可以是中心工作台移动式结构或双动柱龙门移动式结构。龙门采用单个龙门上配备两个滑枕的设计,每个滑枕分别带有一个五轴摆头,其中一个滑枕用于超高压水射流切削,另一个用于传统的高速切削。CMC只需一次安装即可完成机翼蒙皮的所有精加工:裁切、钻孔、切削、表面铣削、标记和检测,使工件离开机床后可以直接进行装配。该机床被全球的空客合作伙伴广泛使用。
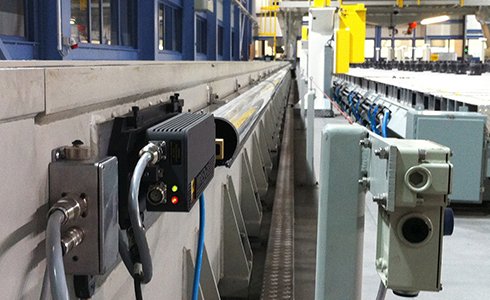
模块化CMC提供6-50 m长的标准X轴及定制尺寸。“过去我们总是在X轴上使用钢带栅尺,而安装在机床上的光栅尺长达30-50 m,这会导致结构性问题,并且使热补偿变得更加困难,”Flow高级电气项目工程师Todd Fuchs解释道。“即使在装有空调的厂房,在130小时的加工周期中,机床在超过40 m长的范围内,温差也比较大。光栅尺本身与机床基体变化之间,误差因素过于复杂。HS20激光尺提供了在这种长轴上获得精确反馈的最简便的方法。”
CMC通过其龙门两侧的齿条和小齿轮传动装置,利用两侧分别配有激光尺的独立工作的X轴反馈,按主从定位的方式工作。激光尺放置在传动系统附近防护罩下面的导管中,管中通有洁净、干燥的空气,确保获得稳定的测量值,并防止空气中可能的碎片引起激光束“断光”。
Flow共有24条机床轴采用了雷尼绍的HS10激光尺和其替代产品HS20。在雷尼绍工程师的帮助下,Flow已在德国、西班牙、法国以及英国的工厂完成激光尺安装。这两种激光尺均采用相同的激光干涉测量技术。该技术被机床校准专家用于线性误差测量和补偿,不同之处在于激光尺取代了玻璃/钢带配件和细分装置,作为机床的永久栅尺。
与钢带栅尺或玻璃栅尺不同,激光尺系统不具有在长轴上“累积”的短期误差,并且其1 m/s的测量速度能够适应当今快速运动的机床。HS20按IP43的标准密封并经过硬质氧化处理,可在恶劣的加工环境中提供全面保护。“40 m龙门的X轴可重复性技术指标为0.0381 mm,基本等同于机床校准所用的激光干涉仪,” Fuchs说道。“同时,激光尺的分辨率是钢带栅尺的两倍,而同一尺寸和类型的其他机床无法利用这一分辨率。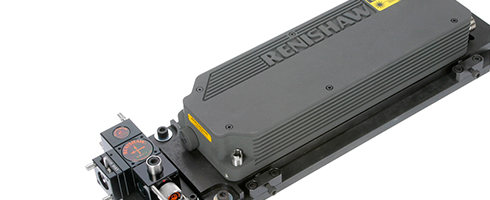
工件测量对安装和序后测量起着决定性作用
X轴定位精度是工件测量的另一要素,对切削过程至关重要。CMC使用雷尼绍RMP60触发式测头在安装过程中对工件进行定位,并在加工后确定最终尺寸。“机翼蒙皮等部分工件在加工前的价值就高达近100万美元,” Fuchs强调说。“这些工件在刚放置在机床上准备加工时,极少与CAD模型吻合,因此我们在加工前要进行全面测量,并完成大量的最佳拟合计算。”该触发式测头设计精巧,能够到达并测量机床主轴可接触的工件加工的任意点。RMP60的无线电跳频 (FHSS) 信号传输系统允许多测头系统和其他工业设备在“嘈杂”工业环境中共存,尤其是在无线Wi-Fi和蓝牙通信普遍应用的环境。
“我们在欧洲许多国家工厂的机床上都装配了激光尺,事实证明雷尼绍HS20激光尺比钢带栅尺更容易安装,并且牢固可靠,”Fuchs补充道。“对于用来切削昂贵和关键工件的具有长轴的机床,客户都希望X轴的定位精度能达到线性测量的最高精度标准 — 激光干涉仪的精度水平。激光尺与RMP60测头配合使用,我们能够给客户带来实实在在的利益。”
背景
与传统的铝合金结构相比,复合材料强度高、重量轻,能够极其精确地制作出所需形状,因此具有明显的优势。这些优势包括:重量轻,降低飞机油耗;在飞机服务期间,
避免了频繁进行腐蚀检查,减少了飞机维护次数。在过去20年间,随着飞机设计的更新换代,复合材料零部件越来越多地取代了由传统材料制成的零部件。
但是,由于复合材料具有超强度纤维和较弱基质,用传统加工方法加工面临着难题 — 传统工艺产生的高温可能会导致材料分层和损坏。磨料水射流切削可以避免这些问题。Flow International在开发此项技术和生产此类设备方面处于世界领先地位。