序中控制
主动型制程控制可以提高精密加工的首件成功率,一次性加工出合格零件。
Productive Process Pyramid™(高效制程金字塔解决方案)序中控制层的控制元素被嵌入金属切削过程中。这些主动型控制可以自动响应实体条件、制程中固有的不确定因素和意外事件,从而降低制程的不稳定性。
在切削过程中进行控制
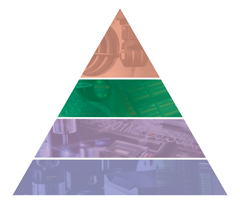
Productive Process Pyramid(高效制程金字塔解决方案)序中控制层处理加工中固有的不确定因素的来源,例如刀具磨耗和温度变化,在加工过程中提供智能反馈和决策。
这些是应用于金属切削过程中的主动型控制。
序中测量能够...
- 使金属切削适应加工过程中的不确定因素,例如工件变形、让刀和热漂移效应等
- 根据实际实体条件,更新坐标系、参数、偏置及逻辑程序流
刀具破损检测识别...
- 刀具是否存在
- 刀具位置 — 以确保未发生拉伸情形
- 刀具破损和/或崩刃
主动型控制
主动型制程控制可提高精密加工的首件成功率,一次性加工出合格零件,因此机器不需要过多地留给返工及重制工件使用。
自动化序中测量意味着机器不再需要等待操作人员的手动指令进行重启操作。
序中测量让您的机床具备自我判断与决策能力,从而实现全自动化加工、提高生产效率。
雷尼绍的工件检测测头、TRS2刀具识别系统和Productivity+™软件能够自动反馈实际的实体条件及环境条件,适时调整金属切削作业。
文档
-
样本: 借助专家级过程控制技术,优化您的制造性能
生产过程控制的测量解决方案